The advancement of modern technology in all industries, especially the textile industry, has made material control increasingly essential. From the receipt of raw materials to the final product, ensuring quality at every stage of the process is essential.
Specific Properties of Quality Control
1. Geometric Properties
Weight
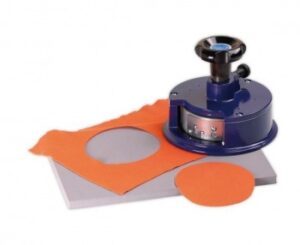
The grammage or weight of the fabric is a key parameter, as it determines the amount of material used in its manufacture. It is expressed in grams per square meter and can also be transformed into weight per linear meter.
The test to determine the grammage is simple: a scale and a circular cutter are used to obtain a 10 x 10 cm sample, which is weighed, and the result is multiplied by 100 to obtain the weight per square meter. This procedure follows the UNE 12127 standard.
Tissue Density
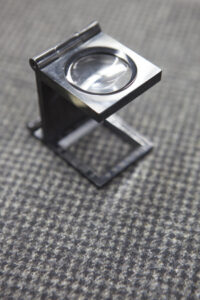
The density of fabrics is measured in threads and picks per centimeter. It is determined by direct observation and counting with a thread counter, an instrument that magnifies the view and delimits the measured length.
Ligaments
The weave defines the interlacing of the warp and weft threads in woven fabrics. Its correct execution is verified by direct observation using a thread counter. The applicable standards are UNE 40017 and UNE 40161.
Dimensional Stability
For fabrics and garments that require dimensional stability after washing, a test is performed in a standard washing machine or on specific equipment such as the Wascator.
50 cm is marked in the warp and weft directions, washed at 40°C using a standard program, and after drying, the length is measured again. The variation, expressed as a percentage, indicates the fabric’s stability (maximum allowable: 3%).
Tissue Deformation and Distortion
UNE 40.079 describes methods for evaluating deformations between warp and weft, which must form a right angle. The following defects may occur:
Warp or weft bowing: the threads are not aligned straight.
Double bowing: the weft bowing changes direction in different areas.
Skew: the warp and weft do not form a right angle.
The measurement is performed with a ruler and set square on a sample conditioned for 24 hours in a controlled atmosphere.
In these cases, on the sample or piece previously conditioned for at least 24 hours in the normal testing atmosphere, the maximum amplitude of the deformation is determined using a ruler and a square graduated in centimeters and millimeters.
Figure 1 shows the operating procedure for measuring the arched warp, as the greatest perpendicular distance existing between the line connecting two points separated by 250 mm from the fabric edge.

Similarly, to measure the greatest perpendicular distance between the line connecting the two ends of an arched weft and the most distant point from it, the graduated ruler (Figure 2) is placed across the fabric so that one of its edges intersects the selvedges along with the determined weft. The square is slid, and the maximum arrow of the mentioned weft is checked concerning the ruler.

Double arching is measured as the shortest side of the rectangle capable of containing the Z-passed section, such that the other side of the rectangle is parallel to the line joining the two points where the weft intersects the selvedges. (Figure 3)
The skew is measured as the distance between the end of a weft and the point on the same selvedge intersected by a line coming from the other end of the weft and perpendicular to the warp (Figure 4), expressed as a percentage of the fabric width.
2. Mechanical Properties
Tensile Strength
This test measures the force required to break a fabric, determining its proper use. It also evaluates its elongation under tension.
A dynamometer is used to apply force until the fabric breaks. The test can be performed on the fabric itself, on seams, or on tear resistance.
Wrinkle Resistance
Wrinkle analysis evaluates a fabric’s ability to recover its shape after being subjected to pressure and bending. This test follows the UNE-EN 22313:1993 standard.
Snagging Resistance
It is performed according to ASTM standard 3939, especially for knitwear. The fabric is placed on a rotating cylinder in contact with a spiked ball. After a specified number of cycles, it is visually compared to a standard scale, assigning a score from 1 to 5 (5 being the highest strength).
3. Retentive Properties
Fabric Fastnesses
- Light fastness: color resistance to sunlight (UNE-EN-ISO 105 B02 Standard).
Washing fastness: measures color resistance to washing (UNE-EN-ISO 105 C06 Standard).
Rubbing fastness: evaluates color resistance to rubbing (UNE-EN-ISO X12 Standard).
Ironing fastness: measures color stability at high temperatures (UNE-EN-ISO 105-X11 Standard).
Fastness to water, perspiration, bleaching, and dry cleaning: are evaluated under specific standards such as UNE-EN-ISO 105 E01 and UNE-EN-ISO 105 E04.Fastness tests are performed in a light box, where samples are compared with color standards under controlled lighting (D65).
Abrasion Resistance
It is measured according to the UNE-EN ISO-12947 standard, determining the number of cycles required to break the fabric threads or calculate the loss of mass. The Martindale abrasion tester is used.
Pilling Resistance
Pilling is the formation of small balls on the surface of a fabric due to friction. It is evaluated using the Martindale abrasion tester according to UNE-EN-ISO 12945-2.
The resistance is classified on a scale of 1 to 5 (5 being no pilling).
4. Waterproofing and Breathability
Air and Water Impermeability
- Air permeability: measured using a permeability meter according to standard UNE-EN 9237.
Water impermeability: evaluates the amount of water the fabric resists before the third drop appears (standard UNE-EN 20811).
Water Repellency
It is measured with the Spray-test according to the UNE-EN 24920 standard, comparing the fabric with a standard.
Breathability
The resistance to the passage of water vapor is analyzed using the UNE EN 31092 (ISO 11092) test, evaluating the thermal comfort of the fabric.
5. Additional Properties
Thermal Insulation
Specific tests are performed to predict the thermal behavior of the fabric under different environmental conditions.
Effectiveness of Oil-Repellent and Water-Repellent Coatings
- Water Repellency: 3M Test II Method. The water repellency value of a fabric is the highest numbered test liquid that does not wet the fabric for a period of 10 seconds (the test liquids used are water and alcohol mixed in different proportions). A higher number indicates greater repellency, evaluated using the 3M Test II method using water and alcohol mixtures.
Oil Repellency: Standard: AATCC 118:1984. The AATCC oil repellency value of a fabric is the highest numbered test liquid that does not wet the fabric for a period of 30 seconds (the test liquids used are hydrocarbons of different molecular weights).
Antibacterial Staging
The test follows ISO 20743:2007 and determines the fabric’s ability to inhibit the growth of microorganisms.
Resistance of Laminates and Bending
Using dynamometry, the cohesion of a laminated fabric is analyzed, determining the adhesion force between layers.
UV resistance
UV-Standard 801-1998 assesses the fabric’s protection against ultraviolet radiation, considering its degradation with use.
Fire Resistance
The tests evaluate ignition, flame spread, heat emission, smoke production and droplet release.
Aging in Climatic Chambers
The fabric’s behavior is analyzed under temperature and humidity cycles to evaluate dimensional stability, color changes, and brightness.
Touch Assessment
The Kawabata Evaluation System (KES) allows the quantification of the feel of the fabric based on variables such as tension, shear, bending, compression and surface.