The Threads

Finishes and Characteristics
Threads are fundamental in the textile industry and can undergo various treatments depending on their intended use. These processes enhance their strength, appearance, and functionality, allowing them to adapt to different applications in clothing and other textile uses.
Below are some of the most common finishes applied to threads:
- Twisting: It consists of joining several threads into one by twisting. This process increases their strength and durability, making them more suitable for fabrics that require greater firmness.
- Singeing: The thread undergoes a thermal treatment to eliminate surface fuzz. This process is especially useful for cotton threads and is usually a preliminary phase to mercerization.
- Mercerization: It is a chemical process in which the thread is exposed to a caustic soda solution. As a result, the thread acquires a characteristic shine, improves water absorption, and becomes more resistant.
- Dyeing: Color is applied to the thread through various dyeing processes, achieving a wide range of shades and finishes according to the final product requirements.
Did you know...?
Torsion is a key factor in the properties of the thread. It is measured by the number of twists per meter, and its level influences the characteristics of the material. A thread with higher torsion tends to be rougher, more compact, and stronger, while one with lower torsion is softer and bulkier.
These treatments allow threads to be used in various applications, from everyday textiles to specialized technical fabrics, ensuring quality and durability in every product.
The Fabrics
We can classify fabrics as follows:
Woven Fabrics

These fabrics are obtained by interlacing two groups of threads:
- Warp: Threads arranged longitudinally.
- Weft: Threads that cross horizontally.
The way these threads interlace is known as weave, which determines the appearance, texture, and strength of the fabric.
Types of fundamental ligaments:
Taffeta (or plain)
It’s the simplest, with a 1-1 structure, meaning each weft thread passes alternately over and under each warp thread. This fabric is reversible, as it looks the same on both sides.

Sarga
Its most common structure is 2-1 or 3-1, meaning that two or three weft threads pass over the warp before alternating. It is characterized by its diagonal lines on the surface.

Raso
To be considered a satin fabric, it must meet two conditions:
- 1
The number of warp and weft threads cannot be equal.
- 2
The warp and weft threads can be any number except 1.
Examples of satin structures include:
One of the most widely used derived weaves is Batavia twill, a variant of twill with a more complex weave pattern.

Knitted Fabrics
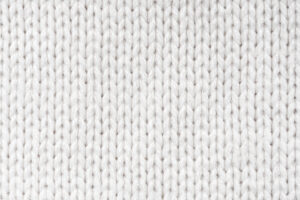
They are made from interwoven threads in a mesh-like pattern, giving them great elasticity and flexibility. They are widely used in clothing due to their ability to adapt to the body.
Nonwoven Fabrics

They are manufactured by joining fibers arranged in layers or webs, without the need for interlacing threads. They are used in products such as felts, industrial filters, and medical textiles.
In conclusion, the structure of the fabric directly influences its properties and uses. From woven fabrics with their various configurations to knitted fabrics and nonwovens, each has specific applications within the textile industry.
Ennoblement Processes:
To improve the aesthetics, durability, and functionality of a fabric, it must undergo a series of specific treatments. These processes vary depending on the fibers that make up the fabric and are divided into several stages, ranging from preparation to final finishing.
Preparation Operations
Before applying dyes, prints, or finishes, it is essential to remove natural and added impurities from the fibers. These impurities can be classified into two types:
-
Natural impurities: These are inherent to the fiber, such as waxes in wool or gums in plant fibers.
Added impurities: These are added during the spinning process, such as oils or adhesives.
Depending on the type of fiber, different cleaning and conditioning techniques are applied:
Singing: This involves removing protruding surface fibers from the fabric by holding it close to a flame, preventing the formation of lint.
Desizing: Substances added during the manufacturing of the yarn or fabric are removed.
Scouring: Water-insoluble impurities are removed using chemical agents.
Mercerizing: A process applied to cotton to increase its luster, absorption capacity, and resistance, making it easier to dye.
Washing of animal fibers: In the case of wool and silk, fats and waxes must be removed with specific detergents before processing.
To obtain light or white colors in natural fiber fabrics, bleaching is performed, which can be optical or natural. Optical bleaching enhances the white color under ultraviolet light, while natural bleaching does not.
Textile Dyeing
Dyeing is a key process in the textile industry, allowing fibers, yarns, fabrics, or finished garments to be colored. Two main methods are used:
Exhaustion: The textile material is immersed in a dye solution until it is completely absorbed.
Impregnation: The dye is applied to the fabric and then passed through cylinders to remove excess dye before the final wash.
Several factors affect the success of dyeing, such as pH, temperature, exposure time, and process speed. Some common defects include unevenness, spotting, or lighter spots on the fabric.

Textile Printing
If designs or patterns are to be applied to specific areas of the fabric instead of dyeing it completely, printing is used. The process consists of several stages:
Fabric preparation (bleaching, mercerizing, scouring, etc.).
Preparation of the color paste.
Application of the color to the fabric using a machine or manual process.
Color fixation using heat, steaming, or other methods.
Washing and final treatments.
To achieve accurate printing, it is essential that the paste has the appropriate viscosity; otherwise, the design may blur or bleed into the fabric.
The main printing methods include:
Direct printing: The color paste is applied directly to the fabric.
Etch-on printing: Corrosive dyes are used to create patterns on dark backgrounds.
Reserve printing: A protective paste is applied to certain areas of the fabric before dyeing, preventing them from absorbing the color.
Sublimation printing (transfer): The design is first printed on paper and then heat-transferred to the fabric.
Digital printing: High-precision printers are used to apply the design directly to the fabric.
These techniques can achieve effects such as flocking, puffy finishes, lamination, or even glitter applications.
Finishes and Sizing
Once the fabric has been washed, bleached, dyed, or printed, final treatments can be applied to improve its appearance and performance.
Mechanical finishes
These treatments involve the use of heat, pressure, or tension to modify the fabric’s characteristics. Some examples are:
Calendering: Pressure, temperature, and humidity are applied to increase shine or improve ironing.
Embossing: A design is engraved on the fabric’s surface using raised cylinders.
Brushing: The fabric’s surface is sanded to give it a peach-skin feel.
Napping: The fibers of the fabric are raised to increase its fluffiness and softness.
Chemical finishes (Sizings)
These treatments involve the application of chemicals to give the fabric special properties. Some of the most commonly used include:
Water-repellent finishes: Repel water and moisture.
Antibacterial and fungicidal finishes: Prevent the growth of microorganisms on fabrics.
Flame-resistant finishes: Make the fabric fire-resistant.
Ultraviolet finishes: Protect against solar radiation.
Antistatic finishes: Reduce the buildup of static electricity.